
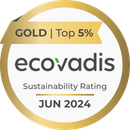
Introduction
In 1983, Astroseal began developing a unique lightning and EMI/RFI protection system. Selected for use on the Bell Boeing V-22 Osprey tiltrotor military aircraft, Astroseal introduced the Astrostrike® brand of materials for lightning strike protection (LSP).
Since then, nearly all composite aircraft trust Astrostrike® for both shielding and lightning protection for the critical task of protecting their aircraft and systems from the damaging effects of lightning strikes.
Military and commercial composite application designers trust Astrostrike® for protection on both large areas of the fuselage, wings, empennage, as well as critical smaller areas including engine nacelles, propellers, winglets and the rotor blades.
Astrostrike® goes beyond composite aircraft, supporting the Wind Power market for large diameter rotor blades and other critical areas of the wind turbine.
Our unique materials technology supports critical industries such as Energy Storage and Fluid Filtration.